Replacing piping and industrial air filtration systems can be a daunting task, especially when you have to shut down your operations. However, these components are the backbone of your industrial system so it’s crucial to maintain them regularly.
The question is — how can you coordinate this without causing unwarranted production delays?
In this article, we outline the common challenges associated with upgrading an industrial piping system and also explore how to streamline the process. Whether you're a plant manager or an engineer, our insights will provide practical solutions to ensure your next upgrade is efficient and effective.
Routine maintenance cycles
Routine shutdowns are crucial for maintaining your equipment and extending its service life. By conducting these planned shutdowns, you can reduce the risk of unexpected breakdowns, improve overall performance, and optimise energy efficiency.
Shutdowns generally have two objectives. Firstly, repairing any problems that were identified during previous shutdowns or standard operations. Secondly, inspecting parts that are not accessible during operation, allowing you to identify any potential problems in the future.
How often should a shutdown occur?
Maintenance shutdowns vary in length, depending on the scale of your operations. In major industrial process plants and factories, shutdowns typically happen every one to two years. For smaller plants and workshops, planned shutdowns are recommended at least once every six months.
While problems may arise outside of a planned shutdown and require urgent attention, this should be the exception to the rule. If this is happening too frequently, you will need to adjust your regular maintenance processes accordingly.
Common challenges associated with air piping maintenance
Before planning a full shutdown of your plant or factory, it pays to understand the potential challenges that commonly arise.
Air leaks
Air piping is one of the most common perpetrators of leaks in a compressed air system, adding up to 30% of compressed air energy costs. Fortunately, you can book a leak detection test with our experts, allowing you to identify leaks sooner and replace the affected pipes.
Layout inefficiencies
If your current piping layout is inefficient, you may be experiencing unnecessary pressure complications. Remember, the more distance and turns there are in the system, the higher the likelihood of pressure drops. To optimise your piping, restructure the layout with more straight paths and shorter overall distances.
The Industrial Air Systems installation team will help with this process, with a particular focus on creating a strategic loop. This evenly distributes the air to all the end-use equipment, ensuring consistent air pressure throughout the system.
Air piping material
Plastic piping materials are common but may be susceptible to deterioration when interacting with certain kinds of lubricant oils. This can pose a safety hazard and cause air leaks, impacting the system's efficiency and increasing the likelihood of breakdowns.
Instead, we recommend replacing your plastic pipes with aluminium or stainless steel piping because it is safe, hygienic, and durable. Fortunately, if you need to replace any of your air pipes, you can opt for press-fit piping to streamline the process.
How to reduce the impact of a maintenance shutdown
If you are spending too much time on shutdowns and plant maintenance, there are several steps you can take to reduce this. While regular maintenance is unavoidable, the following tips will help to minimise the impact of lost operational time.
Be consistent and proactive
To ensure your shutdowns run as planned, be sure to schedule them regularly. A full shutdown should happen every one to two years for a major plant and every six months for a smaller plant. This proactive approach allows you to flag any potential problems and factor them into your shutdown schedule.
Make a plan
The key to a successful maintenance shutdown is in the planning and preparation. Senior management will define the project scope and the plant shutdown management team will develop supplementary plans, including for health and safety, logistics, storage protection and equipment demobilisation, and quality assurance.
To ensure your team covers everything, get in touch with our experienced team.
Use backup compressors
When shutting down your air compressor for maintenance, you can hire a backup compressor to keep your factory operational. However, during a full-scale shutdown, note that your compressed air piping will not be operational as this will need to be tested and maintained.
Invest in quality equipment
When compressed air piping systems consist of high-quality components, they will run more efficiently and need less maintenance. To minimise the frequency and length of your maintenance shutdowns, we recommend upgrading your system, particularly any parts that have developed issues or are getting a bit older.
Use press-fit piping
Instead of welding, it may be worth switching to a press-fit system that can be installed with a handheld hydraulic tool. This eliminates the need for hot works permits and simplifies your health and safety requirements, achieving faster installation times.
For example, the Pneupress stainless steel system is a leak-free modular piping system suitable for high-pressure applications and high-temperature applications. This system is up to ten times faster to install than conventional welded piping, resulting in savings of up to 30%.
Coordinate with Industrial Air Systems
By coordinating your maintenance timeframes with our team, we can help mitigate the various challenges. With sufficient notice, we can supply any spare parts you will need in advance and also ensure our servicing experts are available to complete the necessary work.Our experts can also provide help with the planning of your maintenance shutdowns and replacement systems with the following services:
- Air compressor repair service
- Compressed air design layouts
- Compressed air leak detection and air quality testing
- Complete compressed air audit and vibration analysis
Find out more about our servicing and support services >>
Piping and compressed air filtration system NZ
At Industrial Air Systems, we supply a wide range of piping and filtration systems for plants all around New Zealand. We have everything you need for your new or existing air system, including:
- Air Compressors
- Air Receivers
- Laser Cutting Systems
- Air Treatment
- Aluminium Air Piping
- Pneupress Stainless Steel Piping
- Accessories
- Spare parts
Get even more details on the Pneupress stainless piping range in the downloadable brochure. From product specifications to the entire range of Pneupress fittings available, you'll find everything there is to know. We've also included helpful details on the Alu Air aluminium piping range.
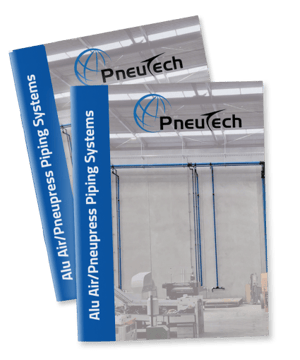