Harrows were facing a number of issues with their compressed air supply. These included:
Dropping air pressure
Multiple machines and tools require compressed air in a factory including spray booths. Harrows were losing CNC machine performance from dropping air pressure which was resulting in a loss of production efficiencies, and spoiled product.
Increased production
They were also expanding manufacturing in their factory by adding the latest technology and high production CNC machinery. This expansion meant they required a higher compressed air supply than what was previously sufficient.
Peace of mind
The Harrows factory compressed air requirements fluctuate according to the type of work being undertaken; they needed to be certain their compressed air supply would be sufficient to cover the highest possible demand. They couldn’t afford for CNC machines to fault during production.
If they were going to upgrade their compressed air system they would also want compressed air redundancy for future proofing.
Optimisation and efficiency
Harrows didn't want an oversized compressed air system that was running ‘offload’ most of the time, using too much energy, and incurring excessive electricity and maintenance costs.
The age of the compressors they had along with continual breakdowns, was contributing to high maintenance costs with one compressor previously suffering catastrophic failure, making repair very costly.
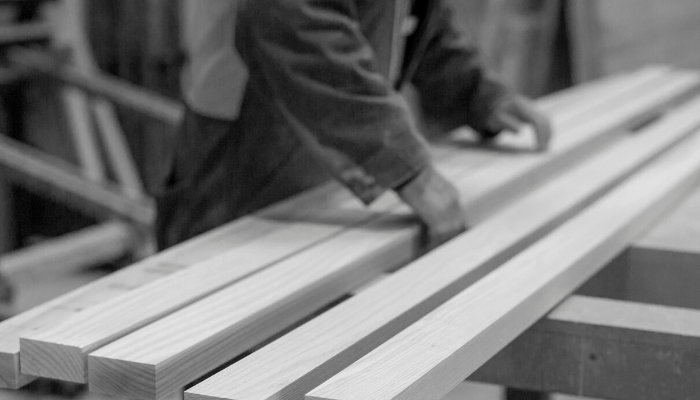