We initially met with the team at South Canterbury Hydraulics to get a better understanding of their compressed air needs. We visited their existing site to view their existing plant and production which gave us a better idea of how they used compressed air. We also discussed future requirements and how their needs were changing due to the shift to a bigger premises.
South Canterbury Hydraulics also had big plans to increase operations – more machinery, workstations and employees meant that their new compressed air system and piping would need to meet bigger demand. From our initial discussions, we were able to get a good understanding of their future compressed air requirements and the products that would be needed to make the new system work for their needs.
We supplied a new variable-speed drive 10hp RSCR10PM Vixen air compressor. Adequate moisture removal drains and filters were also added as well as a full compressed air piping ring main that was installed around the perimeter of the workshop. The air piping ring main was installed at height, with 14 outlets featuring in every working area that required compressed air.
We worked closely with South Canterbury Hydraulics to ensure that the new system was installed on time. There were many trades working in and on the building along with various building alterations being completed while the new compressed air system was being installed, so it was important for us to work quickly. Our Industrial Air Systems install technician worked closely with the team onsite throughout the installation period to keep everything on track and within a very tight completion timeframe.
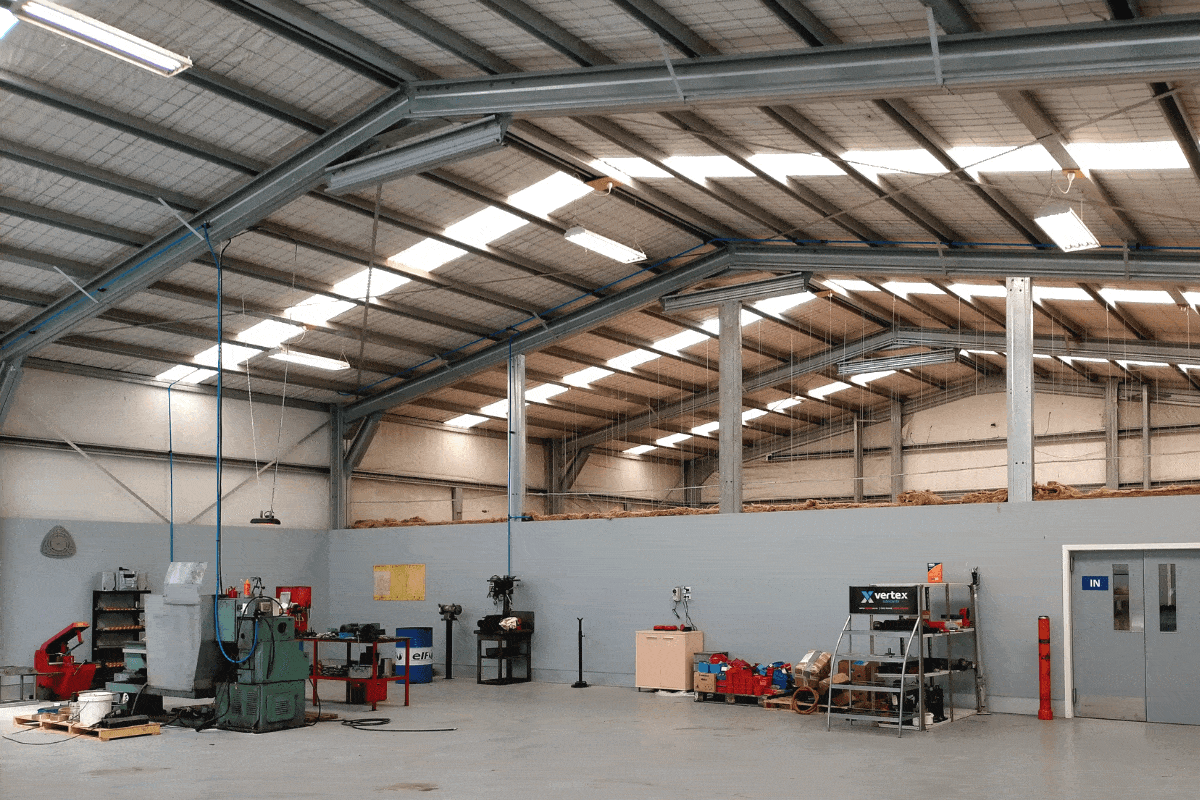
A full compressed air piping ring main, Vixen variable-speed drive compressor and filtration were supplied for South Canterbury Hydraulics.