In process industries, purity requirements for air/gas are usually higher than purity requirements for standard industrial applications. Production of compressed air in process industries usually starts in a conventional compressed air system with standard equipment for the treatment of industrial compressed air/gas.
At a certain point, there is a switchover from industrial to process filtration and from this point on different materials and filtration procedures are applied. Due to contaminants such as solid particles, moisture, hydrocarbons or bacteria compressed air/gas when used in the process can harm and cause quality and efficiency problems.
PneuTech’s range of process filtration are available in 14 bar or 50 bar specifications.
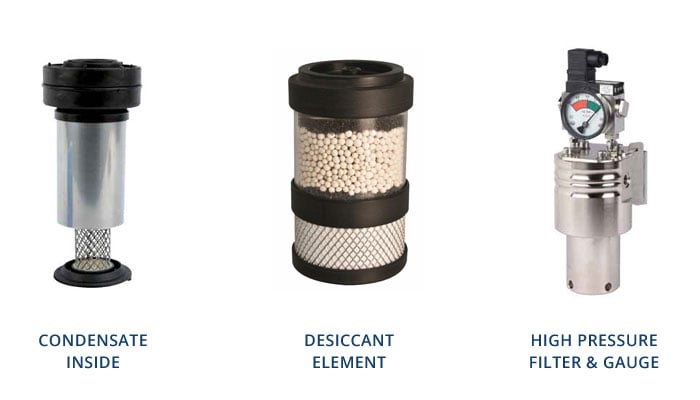
For more information on the range of filtration products available, download our free brochure.
Vacuum filtration M-VAC filters have been developed for medical vacuum applications.
These filters are optimised for the highly efficient removal of bacterial and other contamination (solids and liquids) from the suction side of vacuum pumps preventing damage to the pump and the potential biological infection of the surrounding environment.
Removed liquids are collected in a transparent flask which can be removed for sterilisation. The efficiency of the PneuTech filter elements exceeds the 0.005% penetration specified in HTM 2022 for infectious disease units when tested in accordance with BS 3928.
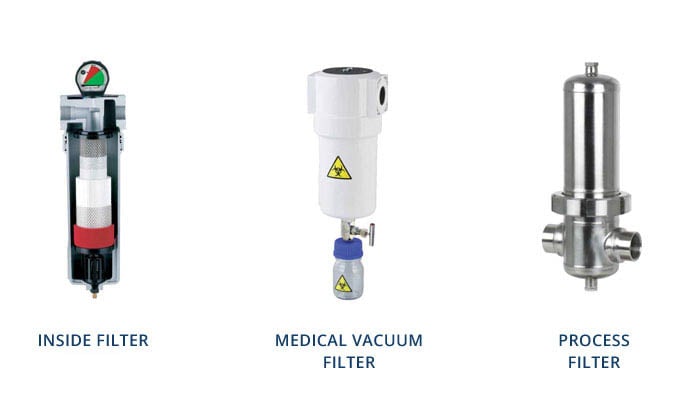
For more information on the range of filtration products available, download our free brochure.
High-temperature filtration?
PneuTech has a special range of filtration for high-temperature applications above 65°C and up to 85°C at 13 bar pressure or 120°C at 10 bar pressure. The filter elements have been designed with aluminium end-caps and special filter material to withstand these higher temperatures.
What is a desiccant element and can it remove moisture?
PneuTech PMS2 two-stage filter elements are designed for separating water vapour from small flows of compressed air, therefore, drying the air. In the first stage, desiccant adsorbs water vapour from the air and in the second stage depth fibre filter media intercepts dust particles. Filtration grade MS2 is suitable for point of use application and can achieve Class-1 (solid particles) or Class-2 (water) air supply for standard ISO8573-1. It is important that inlet air is free of liquid water and oil aerosols. Elements should be changed 12 monthly or sooner according to regular air quality testing. Suitable for up to 459cfm flow rate at 7 bar pressure.
Medium or high-pressure filtration?
Medium pressure (50 bar) and high pressure (100 bar, 250 bar, 420 bar) filtration is a very specialist product requiring precision engineering to ensure the safety of your staff and equipment. PneuTech supplies a high-efficiency range of filtration for these applications, which can be used in the automotive, electronics, food & beverage, chemical, petrochemical, plastics or paint industries.
How do condensate separators work?
Cyclone condensate separators use centrifugal motion to force liquid water out of compressed air. The spinning causes the condensate to join together on the walls of the centrifugal separator. When the condensate gains enough mass it falls to the bottom of the separators bowl where it pools in the sump until it is flushed out of the system by the automatic float drain valve. They are installed following aftercoolers to remove the condensed moisture.
Learn more details about the filtration products available, check out the free brochure here.