This company needed an experienced compressed air supplier that could also provide regular maintenance services to avoid future breakdowns of vital factory equipment. We had previously been engaged to service and maintain this company's compressed air system, which included 3 screw compressors, refrigerated dryers and their 30 bar compressed air set up. Due to our local reputation of providing reliable service and a fast turnaround as well as access to global resources as part of the PneuTech Group, we were also asked to assist with the filtration breakdown.
This company needed to get back up and running as soon as possible so being able to provide them with a guaranteed one hour service turnaround, 24/7, 365 days a week was also crucial to this business. We were able to send out a compressed air technician to their factory to find the faulty filtration element and provide some next steps to get the factory back up and operating.
With the best interests of the business in mind, our first approach was to try and source a replacement part for their failed filter sourced from an overseas supplier, with an unknown brand. After trying all of PneuTech Group's global suppliers, as well as local competitors in Australia and New Zealand, we realised that the only solution was to supply a new filtration set-up and ultra-fast at that!
We sourced a European made PneuTech filtration system that featured second-to-none quality and performance, with a design pressure of 50 bar. Complete with auto condensate drains and differential pressure gauges to help inform factory staff of when elements reach saturation point and need replacing (to avoid failure again), the new filtration provided a higher efficiency and more reliable filtration solution than what the business had previously.
With only three days to go, we worked with our suppliers into the weekend to get the job done. DHL couriered an entirely new 3-stage Class-1, 30 bar filtration set-up into the factory. The filtration was delivered and re-fitted to the existing high pressure air line system and made operational inside the given timeframe. Pictured below is the new PneuTech filtration system and elements used in the new filtration set-up.
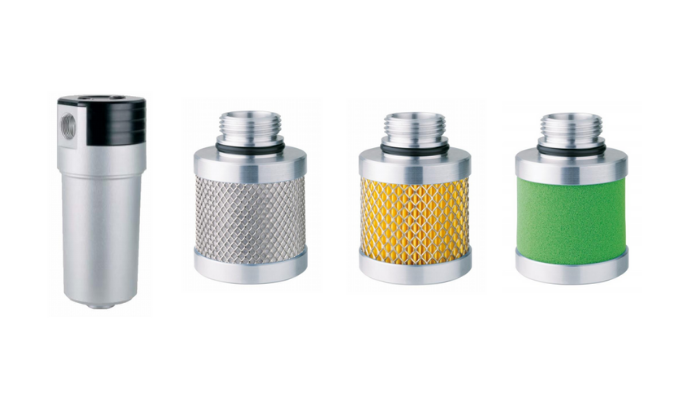